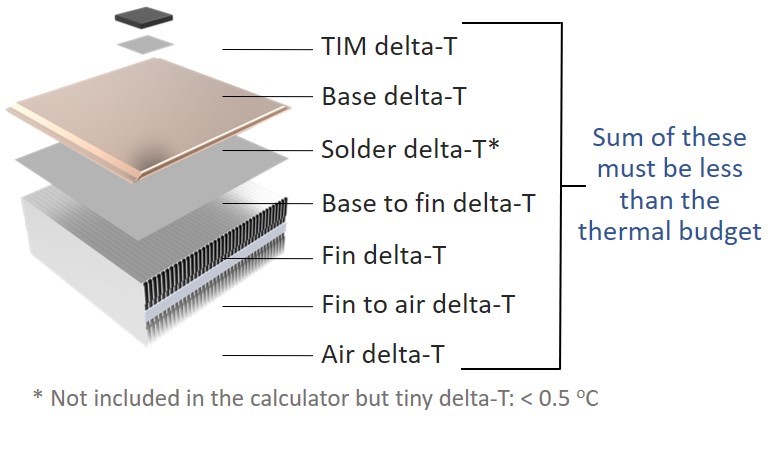
Following is an example using this formula to show optimum fin spacing. In both cases it may be seen that there are limits to how much heat sink thermal resistance may be reduced by either increasing fin.
If you are in the early stages of heat sink design and need an estimate of the required heat sink size refer to this online calculator.
Heat sink fin spacing calculator. This heat sink size calculator will calculate the heat sink width and number fins required to maintain a specified heat source temperature for a heat sink cooled via natural convection and radiation. The heat source is assumed to cover the entire base of the heat sink. The heat sink size calculator first calculates the optimum spacing between the.
Heat Transfer by Convection of a Heat Sink with Fins Calculator and Equations. Fins are used to increase heat transfer area and provide a cooling effect. However if hA Pk is greater than 100 the fins will insulate and prevent heat flow.
H air film convective coefficient. A exposed surface area of the fins. Heat Sink Calculator 1.
Length - up to 500mm 2. Fin Thickness - ranges from 02-06mm 3. Fin Spacing - should be at least 2X the fin thickness 4.
Fin Height - between 3-100mm. Watch fin efficency - dont make the fins taller than useful. Materials - aluminum or copper.
Both can be nickel. The heat sink size calculator is based on a well-established equation for estimating heat sink volume during the early stages of heat sink design. A reference link has been placed below the calculator for further reading.
In our experience it generally estimates the overall heat sink volume within - 15 of a final design. For assistance optimizing heat sink dimensions materials and fin. The the width W of the heat sink spacing between the fins s and number of fins N will then be calculated for the selected values of L and H.
The convection heat dissipation Q c1 from area A 1 the external side surfaces of the heat sink shown figure 2 is first calculated. How does the Heat Sink Calculator Work. This tool is designed to calculate junction temperature of an electronic device typically power devices given four parameters.
The maximum ambient temperature the devices junction-to-package thermal resistance the thermal resistance of the heat sink and the power applied. It can also calculate the maximum power that the device can. If you were to try to optimize the heat sink dimensions the spacing between the fins would be a very small value since the air velocity and hence rate of cooling increases with decreasing fin spacing.
In real world applications the flow is supplied by a fan or blower. The flow rate would not be fixed it would be limited by the increase in pressure drop across the heat sink that would occur as. Heat Sink Calculator is a software tool for designing analysing and optimizing heat sink performance.
The thermal resistance of the heat sink and temperature of the power source is calculated. The user can choose between natural or forced convection andor radiation for the modes of heat transfer. Heat sink typically has a fin spacing of 6 mm significantly greater than the optimum of 28 mm.
It will be necessary to use bonded or swaged fins. Such a heat sink will cost more but will. 9 Temperature at the base of the heat sink as a function of fin spacing 12 10 Conductance of the heat sink for different fin thicknesses 13 11 Temperature at the base of the heat sink for different fin thickness 13 12 Heat transfer from the heat sink for different fin thicknesses 14 13 Conductance of the heat sink for different fin height 14.
UNCLASSIFIED Approved for public release. Following is an example using this formula to show optimum fin spacing. Length of heatsink direction of gravity5 in.
127 mm Dynamic Viscosity014410-4 lbft sec. 560 K 38C Estimated fin temperature rise. 100F 555C Gravity322 ftsec 2.
The heat sink height and length are fixed in the demo version. The full version allows you to vary all the parameters shown in the demo version as well as save and retrieve analyses filesSelect a sample analysis below to get started. For purposes of illustration these equations were used to estimate heat sink thermal resistance for a 50 x 50 mm aluminum heat sink.
The effect of increasing the fin height and the number of fins is shown in Figure 2 for a constant air velocity and in Figure 3 for a constant volumetric flow rate. In both cases it may be seen that there are limits to how much heat sink thermal resistance may be reduced by either increasing fin. If you have optimum spacing you can get the heat transfer coefficient from the s-based nusselt number.
Nus hsk where h is the heat transfer coefficient and k is the conductivity of the fluid - not the heat sink then to get the total heat transfer from the array use. If you are in the early stages of heat sink design and need an estimate of the required heat sink size refer to this online calculator. Fin Pack Information While fin height can vary considerably by application we typically see figures in the 10-35 mm range.
Fin thickness for fin packs zipper fins range from 02 to 06 mm while fin spacinggap should be at least 2X the fin thickness. Next input the fin pack. Program based in Microsoft Excel calculates the optimal fin spacing and efficiency a whole heat sink efficiency heat dissipation and the maximum heat sink temperature based on the input parameters fin length fin height fin thickness fin material maximum allowable temperature and ambient temperature.
ET Heat Sink V10 This module is an Excel COM Add-in. It has the following features. A fin n ed heat sink temperature distribution can be determined given heat sources.
Fin spacing height and thickness. Steady state or transient solutions are available for forced are natural convection. For a relatively large heat sink that is 203203 mm square a ratio of 0333 yields the optimum combination of individual heat-transfer coefficients and the array surface area.
For a smaller heat sink approximately 7676 mm square the optimum value of the ratio was found to be closer to 050. Kraus and Bar-Cohen Design and Analysis of Heat Sinks.